Navigating the Impact of Tariffs: Insights from Bob Baker
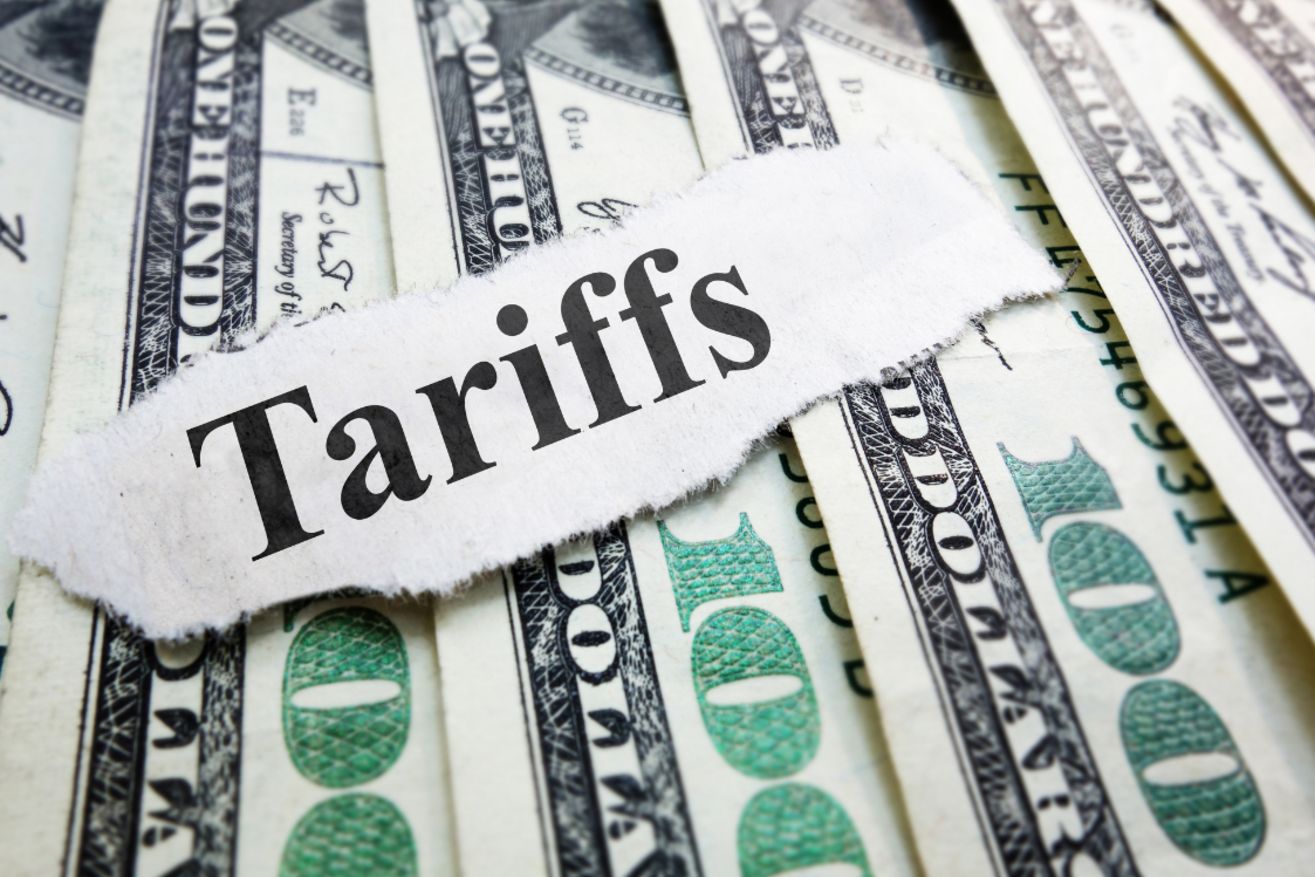
As the 2024 election campaign turned the corner into the final stretch, President Donald Trump began advancing his tariff strategy as part of his broader "America First" agenda. Now, with his second term underway, the prospect of new tariffs looms large. Businesses across the country are left wondering what to expect and how to prepare for an uncertain horizon.
Before diving into the potential impacts of tariffs, let’s first examine what a tariff is and its historical context. At its core, a tariff is a tax imposed on imported goods entering a country or sovereign territory. For centuries, tariffs have served as tools for regulating trade and generating revenue for governments. Typically, the importer—often a merchant or distributor—is responsible for paying the tariff.
In modern economics, tariffs have evolved beyond mere revenue generation. They are often employed to correct trade imbalances and to protect domestic industries by making imported goods less competitive. The economic rationale is straightforward: producers and consumers tend to gravitate toward lower-cost goods of comparable quality. By imposing tariffs, governments can influence this dynamic to favor domestic production. However, tariffs are not without controversy and in some cases can be seen as retaliatory; their ripple effects can be both significant and unpredictable. Today, they’re as much a geopolitical bargaining chip as they are an economic tool. To say the least, it’s complicated.
To gain clarity on the subject, I sat down with Bob Baker, a global logistics and supply chain expert. With decades of experience navigating the complexities of sourcing, transportation, and supply chain strategy, Bob has built and led logistics and tech-based businesses across the globe. He has held executive roles at SynchroNet Logistics and Sealand Service Inc., served on numerous boards, and advised companies in the US and internationally on strategic plans. Currently, Bob focuses on guiding start-ups and established businesses alike, leveraging his expertise in supply chain logistics, asset management optimization, and international transportation. His well-rounded background makes him a highly respected figure in the field.
Here are some insights from our conversation:
Q&A with Bob Baker
Q: What kinds of questions are your clients bringing to you as we kick off 2025?
The top questions typically revolve around preparedness: “How do we anticipate and mitigate risks associated with new tariffs?” and “What’s the best way to build resilience into our supply chain?” Clients are also keenly focused on diversifying their sourcing strategies to minimize exposure to any single country or region.
Q: When we met earlier this month, you spoke of technology and AGI as being an equalizer when facing the impact of tariffs. Can you expand on your thoughts there?
Absolutely. If you see where tech companies are positioning Artificial General Intelligence (AGI), as a mechanism for machine adoption of intellectual tasks and cognitive abilities, one can forecast that it may eventually be utilized in a way to operate performative functions within a supply chain’s operations. This adoption of technology, through the automation of certain key functions, will transform supply chain management and help mitigate the impact of costs associated with tariffs. Secondly, AI in general can be used to research vast troves of data and predictive modelling to provide an outlook and scenario where one can better forecast tariff impacts and optimize sourcing decisions. The advantages of AGI and AI long-term can not only reduce operating costs but also improve efficiency, streamlining SCM across the board, and proactively be used in a way to ensure compliance with ever-changing complex trade regulations. I believe for businesses to stay competitive in the future, adopting these tools isn’t just advantageous; it will be essential.
Q: Are there specific industries you believe will be hit hardest by new tariffs in 2025, and why?
Well, let’s hope that these new tariffs are not implemented as advertised. Many companies in almost every industry were severely impacted operationally and financially by the tariff trade war with China in 2019-2020. However, if these proposed tariffs do go into effect, particularly with our largest trading partners in Canada and Mexico, I would most likely keep an eye on the auto, oil, and e-goods industries. As of late they have been quite susceptible to economic shocks in the market and punitive tariffs would certainly present challenges to companies in these industries, as well as their customers and the consumer in general.
Q: Are there lessons that could be learned in the business community from the impact of the most recent severe China tariffs?
Absolutely. Most, if not all businesses importing from China, suffered from increased transportation and logistical costs during the last major implementation of punitive tariffs. Many companies have been advancing their inventories to the US ahead of any official announcement date of tariffs and ensuring there are enough products available for the customer base. Clearly, swift decision-making in executing alternative sourcing options, and maximizing supply chain capabilities, when necessary, will be on the table in the near term for most companies.
Q: How do you view the interplay between tariffs and ESG (Environmental, Social, and Governance) considerations in supply chain decisions?
That is a very good question. I honestly didn’t connect the two because I’ve usually viewed a company’s ESG position as somewhat of a scorecard of its impact on the environment, treatment of employees, and its level of operating principles and controls. But as I think about it, if a company is slow to adapt and change, it may be in a tough position to correct course as a result of a punitive tariff impacting its supply chain.
Q: What advice would you give to small businesses that lack the resources of global enterprises to adapt to tariff changes?
My recommendation to small businesses in this environment is twofold. First, I would recommend evaluating any departmental functions within their supply chain that could be automated or outsourced to reduce costs to mitigate the impact of tariffs. Secondly, I would recommend evaluating options to integrate a good, well-referenced middleware SaaS SCM solution company that can efficiently connect the small business’ internal ERP to its factories or source locations and manage the small business supply chain from factory to final customer delivery. It can centralize operating expenses for the small business and assist in offsetting punitive tariff changes.
As businesses brace for what’s ahead, one thing is clear: understanding and adapting to the complexities of tariffs will be critical. Whether through strategic planning, technology adoption, or expert guidance, the key is to remain agile and informed. Bob’s insights provide a valuable starting point for navigating this intricate landscape.